Common Maintenance Problems & Solutions: A Guide
Is your business prepared for the inevitable challenges that arise from neglected maintenance? Failing to address routine maintenance issues can lead to a cascade of problems, ultimately impacting your bottom line and operational efficiency.
The world of asset management is a constant balancing act. Organizations strive to maximize the lifespan and performance of their equipment, while simultaneously navigating the complexities of budget constraints, operational demands, and the ever-present threat of unforeseen breakdowns. This intricate dance highlights the crucial importance of proactive maintenance strategies. Neglecting this aspect can have far-reaching consequences, leading to wasted resources, operational inefficiencies, and the potential for costly, unexpected downtime. Routine maintenance, in essence, is the bedrock upon which efficient operations are built.
One of the most pervasive issues in maintenance management is the lack of structure and a well-defined schedule. Without a clear roadmap, teams struggle to prioritize tasks, allocate resources effectively, and anticipate potential problems. This deficiency can manifest in various ways, from a backlog of unaddressed maintenance requests to a reactive approach where problems are only addressed after they've escalated into critical failures.
Consider the situation where maintenance tasks are listed in a generic format, with little more than a "check..." instruction. This vague approach offers minimal guidance on what to inspect, how to assess the condition of the equipment, or the necessary actions to take. Such a lack of clarity not only increases the risk of overlooking critical issues but also hinders the ability to standardize maintenance procedures and train new personnel. The result can be a decline in equipment performance, premature wear and tear, and increased potential for costly repairs or replacements.
Another critical aspect is the correlation between maintenance strategies and unexpected breakdowns. Reactive maintenance, where repairs are initiated only after a failure occurs, may seem like a cost-effective measure in the short term. However, this approach often leads to prolonged downtimes, disruptions to production, and increased repair costs. A proactive strategy, on the other hand, prioritizes preventive maintenance, scheduled inspections, and timely interventions to prevent failures before they happen.
The financial implications of inadequate maintenance are significant. Emergency repairs are typically far more expensive than routine maintenance, and the costs associated with downtime lost production, delays in deliveries, and potential safety hazards can quickly add up. By investing in proactive maintenance, companies can minimize these costs, extend the lifespan of their equipment, and create a safer working environment.
Regular maintenance is not merely an operational necessity; it is a strategic imperative. It extends far beyond the immediate task of fixing a broken machine. Its about protecting investments, maintaining operational efficiency, and ensuring compliance with industry regulations. It's about building a resilient business that can withstand the inevitable challenges of an unpredictable world.
The benefits of a robust maintenance program extend across multiple facets of an organization. The implementation of routine maintenance practices can significantly reduce downtime, a major contributor to lost productivity and revenue. By proactively addressing potential issues, companies can keep their equipment running smoothly and their operations on schedule. Routine maintenance also optimizes resource allocation. By accurately predicting and planning for maintenance needs, companies can manage their budgets more efficiently, ensuring that the necessary resources are available when and where they are needed.
Furthermore, routine maintenance contributes to a safer working environment. Properly maintained equipment reduces the risk of accidents and injuries, promoting the well-being of employees and reducing the likelihood of costly workers' compensation claims. These multifaceted benefits collectively demonstrate the critical importance of a well-planned and implemented maintenance program.
Preventive maintenance, also known as routine maintenance, is an approach that involves regular inspections, servicing, and replacements performed at predetermined intervals, regardless of the equipment's current condition. Scheduled restoration and replacement tasks are two prime examples of this practice.
Maintenance strategies often fall into two broad categories: planned and unplanned. Planned maintenance is carefully organized and executed based on a pre-defined schedule. The implementation of planned maintenance necessitates a comprehensive understanding of equipment behavior and performance patterns to make informed decisions regarding critical work cycles and the timing of replacements.
The following table provides a concise overview of the potential problems that arise from inadequate maintenance. This table serves as a practical guide for identifying potential vulnerabilities and highlighting areas where focused attention is required:
Issue | Potential Trouble |
---|---|
Lack of Structure and Scheduling | Unexpected breakdowns, resource waste, operational slowdowns |
Vague Task Instructions | Inefficient maintenance, potential for overlooked issues |
Reliance on Reactive Maintenance | Extended downtimes, increased repair costs, operational disruptions |
Inadequate Budgeting | Financial strain from emergency repairs, deferred maintenance |
Neglect of Preventive Measures | Premature equipment failure, decreased lifespan |
Failure to Comply with Regulations | Legal ramifications, safety risks |
In the dynamic landscape of operational management, the effective implementation of maintenance strategies is often the critical factor that determines the success or failure of a company. The ability to consistently optimize the performance and lifespan of equipment whilst maintaining a safe and efficient working environment requires a thorough and carefully planned maintenance program. These programs must be designed not just to resolve current issues but also to anticipate and prevent future problems, ensuring operational resilience and sustainability.
This proactive approach involves the strategic scheduling of maintenance tasks before issues arise, thereby significantly reducing the risk of unexpected breakdowns and the associated costs of downtime. Routine maintenance serves as a cornerstone for maintaining equipment health and efficiency across various industries. This encompasses a broad range of actions, including regular inspections, cleaning, lubrication, and timely component replacements. Such activities prevent unexpected and costly surprises, helping to extend the life of the equipment.
The potential impact of poor maintenance practices extends beyond immediate operational disruptions. From a business perspective, the long-term consequences can be equally damaging, affecting financial performance, reputation, and employee morale. Implementing a comprehensive maintenance strategy can minimize downtime, which directly translates to increased productivity and revenue. When equipment operates at its peak performance, companies can meet their targets, respond more quickly to customer demands, and boost their competitiveness in the market.
Companies must understand how to avoid unforeseen equipment breakdowns. A comprehensive plan can prevent costly downtime, extend the lifespan of equipment, and ensure safety and compliance with industry regulations. Investment in proactive maintenance programs can prevent unexpected breakdowns, cut down on repair expenses, and promote a safer working environment. The value of routine maintenance lies in its ability to enhance equipment lifespan, optimize operating costs, and secure the safety of personnel.
To effectively address these challenges, businesses can leverage various strategies, including the implementation of computerized maintenance management systems (CMMS) for task management, setting clear guidelines to prevent ambiguities, and providing staff training to enhance their understanding of the equipment. Furthermore, it's essential to develop a comprehensive preventative maintenance schedule tailored to specific equipment requirements.
In the same vein, fleet management services, such as Universal Fleet Solutions (UFS), can provide valuable insights into equipment performance and average costs, helping organizations make informed decisions and optimize their maintenance budgets. These services bring expertise that ensures all aspects of a company's equipment operations are properly managed and maintained.
It is important to understand that reactive maintenance, while sometimes necessary, should not be the primary maintenance strategy. Relying solely on reactive maintenance can result in extended downtimes when unforeseen problems occur. Proactive maintenance is more than just fixing broken equipment; it is a strategic approach to asset management that aims to prevent failures before they happen.
Furthermore, companies should ensure that their prevention efforts encompass all areas that could potentially give rise to problems. This includes a focus on personnel training and development, the establishment of optimal maintenance practices, a well-maintained hardware and systems infrastructure, and a supportive environment. The proactive maintenance is achieved through organized strategies, scheduled inspections, and the timely replacement of worn components.
While routine maintenance is often predictable, emergencies such as broken appliances, plumbing leaks, or roof damage can significantly impact profits. Addressing these types of unexpected issues requires a robust financial planning and an efficient maintenance system to quickly address problems.
Preventive maintenance, sometimes called routine maintenance, can be defined as an equipment maintenance strategy based on replacing, or restoring, an asset at a fixed interval regardless of its condition.
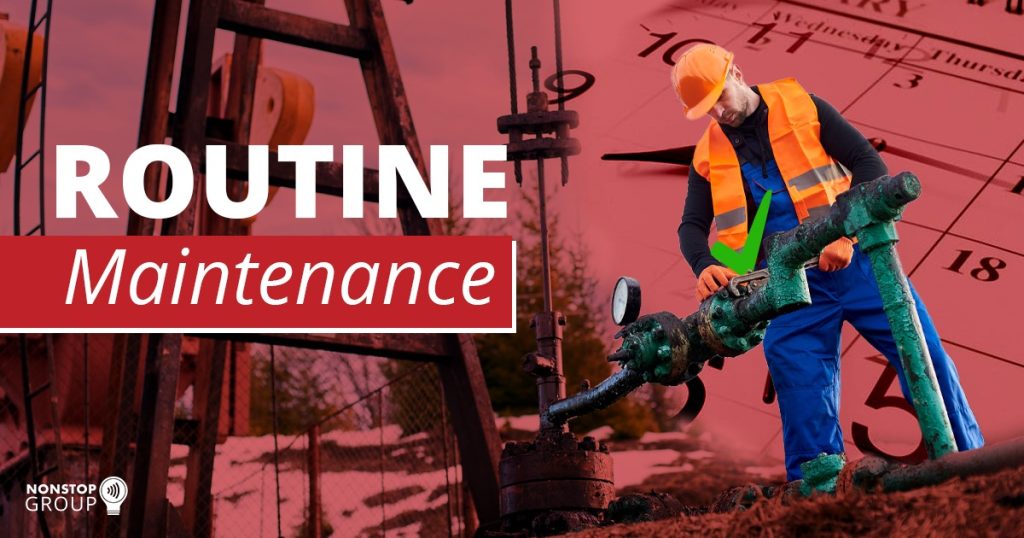
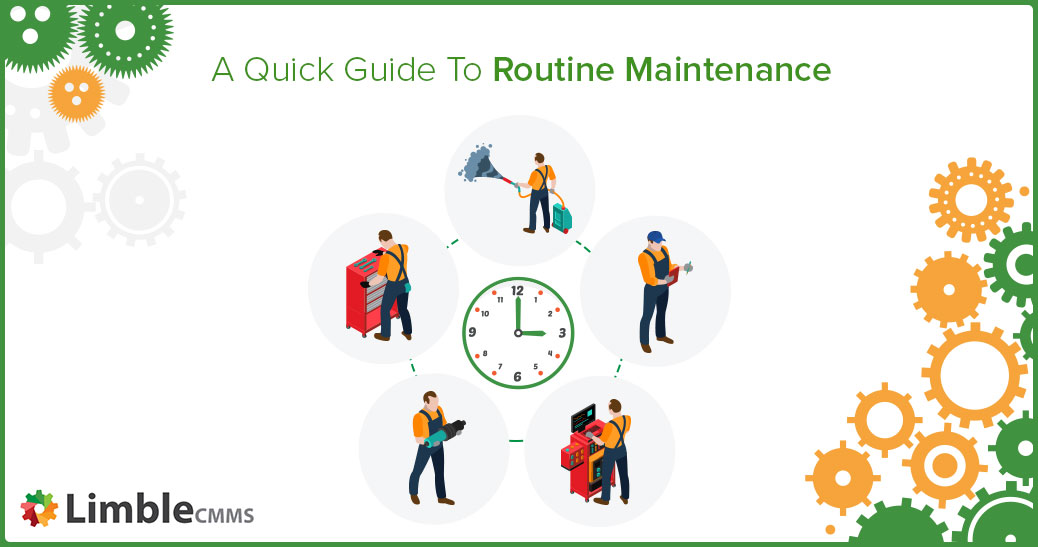
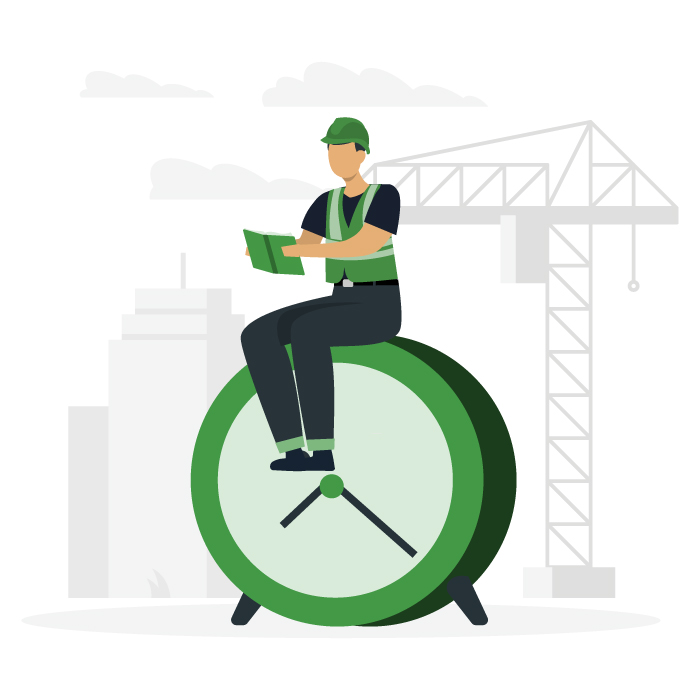